Сварка металлов в домашних условиях
Наиболее распространенными способами сварки в домашних условиях являются газовая и ручная электродуговая сварка. Газовую и электродуговую сварку используют для создания неразъемных соединений металлических деталей посредством сварочного шва. При ручной сварке используют следующие виды сварных соединений: стыковые, тавровые, угловые, внахлестку, прорезные, торцевые, с накладками и пробочные (рис. 1).
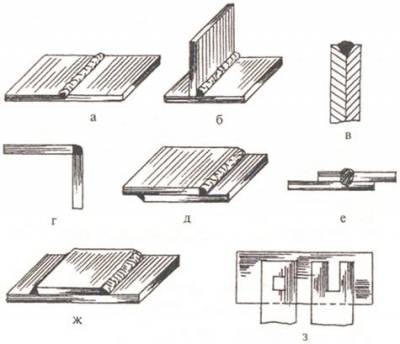
Рис. 1. Сварные соединения: а — стыковое; б — тавровое; в — внахлестку; г — прорезное; д — торцевое; е — пробочное; ж — с накладкой; з — угловое.
Стыковой шов (рис. 1, а) — соединение торцевых поверхностей деталей, иногда отличающихся по толщине.
Угловой шов (рис. 1, з) — соединение двух плоскостей, располагающихся под углом друг к другу.
Нахлесточный шов (рис. 1, в) — соединение, в котором один лист металла располагается на поверхности другого, слегка перекрывая его.
Тавровый шов (рис. 1, б) представляет собой соединение, в котором торец одного изделия приваривается к боковой поверхности другого.
Прежде чем приступать к сварочным работам, нужно тщательно очистить поверхность деталей от грязи, ржавчины, окалины, масел.
Газовая сварка
В качестве горючих газов для газовой сварки применяют ацетилен, водород, пары бензина, природный газ. Все эти газы горят на воздухе, но не развивают при этом высокой температуры, необходимой для сварки, поэтому они сжигаются в струе кислорода. Наиболее удобен и распространен ацетилен. Он образуется в результате взаимодействия воды и карбида кальция. При сгорании ацетилена в струе кислорода температура пламени достигает 3200—3400 °С. Для получения ацетилена служат специальные устройства — генераторы, широко выпускаемые промышленностью. Ацетиленовые генераторы классифицируют по следующим признакам: по производительности — 1,25—640 м3/ч; по давлению вырабатываемого ацетилена: низкого — до 0,02 МПа и среднего — 0,02—0,15 МПа; по способу взаимодействия карбида кальция с водой: генераторы KB («карбид в воду»), генераторы ВВ («вытеснение воды»), генераторы ВК («вода на карбид»). Все генераторы независимо от системы состоят из следующих основных частей: газообразователя, газосборника, предохранительного затвора, устройства автоматической регулировки количества вырабатываемого ацетилена в зависимости от его потребления.
В небольших мастерских широкое распространение получили ацетиленовые генераторы низкого давления ГНВ-1,25, АНВ-1,25-73, среднего давления АСВ-1,25, АСП-1,25-7 и др.
Кислород для газосварки подают из специального кислородного баллона (окрашенного в светло-синий или голубой цвет). Кислородные баллоны должны храниться в лежачем положении.
Для нормальной работы необходимо, чтобы кислород подавался в сварочную горелку равномерно, под небольшим давлением — 3-4 атм. Для этого служит редуктор, который регулирует подачу газа (в баллоне давление 150 атм).
Сварочная горелка представляет собой прибор, в котором ацетилен смешивается с кислородом и эта смесь сгорает.
К горелке при работе подводят шланги — ацетиленовый (от генератора или белого баллона) и кислородный (от синего баллона). Кислород подают под давлением 3-4 атм в центральный канал, и затем через отверстие малого сечения он вырывается наружу с большой скоростью. Струя его создает большое разрежение и засасывает ацетилен, который попадает в горелку под меньшим давлением. Оба газа смешиваются между собой в смесительной камере и оттуда через наконечник выходят наружу.
Наконечники на горелке можно менять в зависимости от толщины свариваемых деталей: чем они толще, тем больше должен быть диаметр канала наконечника.
Перед сваркой подготавливают шов. Для этого свариваемые поверхности очищают от грязи, ржавчины, масла и краски.
Для сварки металла толщиной до 1,5 мм края деталей отбортовывают, высоту бортов делают от 1,5 до 2,5 мм и отбортованные кромки устанавливают плотно, без зазора. При сварке металла толщиной более 1,5 мм отбортовку не производят. Между кромками оставляют зазор от 0,5 до 1 мм. При толщине свариваемых деталей от 5 до 15 мм их кромки скашивают с одной стороны (рис. 2, а), при толщине более 15 мм кромки деталей скашивают с двух сторон (рис. 2, б). Угол раскрытия шва должен быть от 40° до 90°. Скашивают кромки зубилом, на станке или газовой резкой. Между свариваемыми кромками оставляют зазор 1—3 мм.
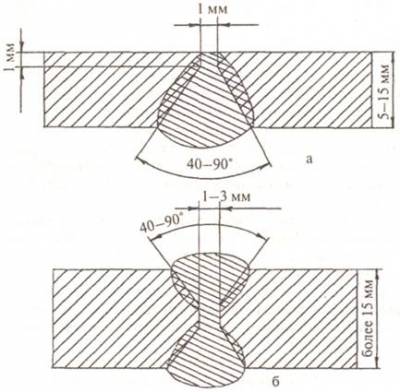
Рис. 2. Сварка металла при толщине свариваемых деталей от 5 до 15 мм (а) и более 15 мм (б).
Сварку осуществляют следующим образом: кромки расплавляют горелкой, а затем в пламя вводят стальной присадочный пруток, который, расплавляясь, заполняет зазор. Передвигая постепенно горелку вдоль шва, производят сварку. При сварке тонких отбортованных деталей присадочный пруток не применяют, а оплавляют отогнутые кромки. При сварке длинных полос сначала прихватывают шов в нескольких местах, а затем его проваривают целиком. Это делают для того, чтобы избежать коробления изделия.
Газовая сварка может применяться для соединения легированных сталей, в составе которых есть хром, никель, титан и другие элементы. Однако нужно хорошо знать свойства и особенности каждого вида этих соединений. Возможность использования газовой сварки в работе с углеродистыми сталями зависит от процентного содержания в них углерода. Чем его больше, тем свариваемость стали хуже, и наоборот.
Газовая сварка цветных металлов и сплавов
В процессе работы с медью возникают определенные сложности: во-первых, она окисляется; во-вторых, обладает высокой теплопроводностью и высоким коэффициентом расширения при нагревании. Поэтому при ее сварке необходимо использовать флюсы и присадки (марганец, кремний) для очищения от образующихся оксидов, а также избегать появления тепловых деформаций, обусловленных большой теплоемкостью металла. Для этого необходимо увеличить скорость сварки. Наконечник при этом должен быть на 1—2 номера больше, чем наконечник для сварки стали. Чтобы разрушить оксидный налет, осуществляют проковку сваренного шва в горячем состоянии. Сварка меди делается в виде стыковых и угловых соединений, причем только в один слой, тавровое соединение используется только при ремонте. Внахлестку медь не сваривается никогда.
Латунь, как и медь,— трудносвариваемый сплав. Выгорание цинка и поглощение газов расплавленным металлом — основные сложности, возникающие при сварке латуни. Вследствие этого снижается механическая прочность соединения. Чтобы устранить этот недостаток, после всего процесса производится проковка швов. Для латуни с содержанием цинка менее 40% осуществляется холодная проковка, для содержащих более 40% цинка — проковка при температуре 650 °С. Нельзя забывать о том, что выделяемые при сварке латуни пары цинка ядовиты, поэтому необходимо защищать органы дыхания.
Бронза представляет собой сплав меди с оловом, алюминием, кремнием и другими металлами. Газовая сварка применяется только для оловянной бронзы, остальные же разновидности этого сплава свариваются дуговым методом.
Работа с алюминием и его сплавами затруднена тем, что на расплавленном участке появляется тугоплавкая пленка. Для ее устранения используют флюсы и присадочную проволоку. Алюминиевые сплавы бывают деформируемые (сплавы с марганцем — AlMn; с магнием — AlMg; термостойкие сплавы с медью типов Д1 и Д6 (дюралюминий) и литейные (различные виды силумина типов Ал2, Ал4 и Ал9).
Метод газовой сварки используется в основном для сваривания литейных алюминиевых сплавов. Чтобы избежать возникновения пористости металла и его сплавов, нужно предварительно подогревать детали и уменьшать скорость сварки, пламя должно быть мягким и ровным. При газовой сварке алюминия делается только стыковое соединение, нахлесточные и тавровые швы производить не рекомендуется, поскольку из них сложно удалять шлаки и остатки флюсов.
Газовая резка
Процесс газовой резки основан на свойстве стали, нагретой до высокой температуры, сгорать в струе кислорода или иного газа. Для резки применяют специальную горелку — резак. Устройство ее почти такое же, как и сварочной горелки, но кислород выходит наружу под большим давлением — до 8 атм. Вместо ацетилена можно применять пары бензина, которые интенсивно сгорают в струе кислорода.
Процесс резки состоит из двух этапов: подогрев металла ацетиленовым пламенем и его резка струей режущего кислорода. В работе на дому можно использовать резаки отечественных производителей: универсальные (Р2А-01, РЗП-01), вставные (РВ-1А-02, РВ-2А-02) и специальные малой, средней и большой мощности (РЗР-2, РПК-2—72, РК-02).
Для ручной резки в настоящее время применяют различные установки. УФР-5 предназначена для порошково-кислородной резки железобетона, работает на пропане или бутане с кислородом. В ее состав входят флюсоноситель на тележке, копьедержатель, резак, крепление для баллонов. УФР-5 способна резать железобетон толщиной до 300 мм. УГПР служит для резки сталей и чугуна, по конструкции напоминает установку УФР-5. Существуют также переносные кислородные резаки («Спутник-3», «Гугарк»).
Большое влияние на производительность резки оказывает положение резака (рис. 3). Если возникает необходимость разрезать лист стали толщиной до 50 мм, резак ставится вертикально, при большой толщине листа — под углом 5° к его поверхности (рис. 3, а). Затем резак наклоняют на 25—30° в противоположную его движению сторону (рис. 3, б). В этом случае металл лучше прогревается и увеличивается производительность резки.
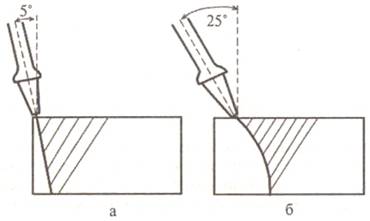
Рис. 3. Положение резака в процессе работы: а — начало резки; б — процесс резки.
Резку поковок и отливок лучше всего осуществлять ручным резаком, который работает на пропан-бутане в смеси с кислородом. Расположение оборудования — под прямым углом к разрезаемой поверхности. На завершающем этапе работы необходимо снизить скорость резки и увеличить угол наклона резака. Разрезание труб производится с использованием ацетилена и его заменителей. Причем скорость резки должна быть достаточно высокой. Способы кислородно-копьевой и порошково-копьевой резки эффективны при прожигании отверстий в бетоне и железобетоне.
Медь и алюминий имеют температуру плавления ниже, чем температура плавления их окислов, и, следовательно, не поддаются газовой резке.
Электродуговая сварка
В быту наибольшее распространение получила ручная дуговая сварка или сокращенно РДС. Она сопровождается плавлением электрода в форме металлического стержня со специальным покрытием при использовании переменного или постоянного тока. В России ее еще называют сваркой плавящимся одиночным электродом, а за рубежом — сокращенно ММА. Ручной сварку называют потому, что зажигание дуги и поддержание ее стабильной длины, перемещение электрода по мере расплавления на соединяемые детали с образованием шва полностью осуществляет сам сварщик.
Электродуговая сварка — это сварка плавлением, при которой нагрев осуществляют электрической дугой. Электрическая дуга представляет собой длительный устойчивый электрический разряд между двумя электродами в ионизированной атмосфере газов и паров металла. На электродах дуги, возбужденной постоянным током, выделяется неодинаковое количество тепла: на положительном электроде (аноде) температура достигает 4000 °С, а на отрицательном (катоде) — 3500 °С. При возбуждении дуги переменным током на обоих электродах температура одинакова и составляет 3500 °С. При сварке постоянным током положительный электрод (анод) присоединяют к детали, а отрицательный — к электроду.
Процесс зажигания дуги происходит следующим образом: в момент соприкосновения электрода с изделием происходит замыкание электрической цепи и по ней начинает проходить ток. Места, в которых возникает электрический контакт, нагреваются сильнее, и под воздействием выделившегося тепла металл расплавляется. При дальнейшем повышении температуры происходит эмиссия — движение электронов под действием теплоты. При этом увеличивается плотность тока эмиссии и проводимость дугового промежутка.
Для осуществления сварочных работ необходимо иметь источник электропитания, сварочный аппарат (трансформатор, сварочные провода, держатель электрода), электроды, защитный щиток для лица, брезентовую защитную одежду, необходимые инструменты (молоток, струбцины и т.п.), противопожарный инвентарь, асбестовый лист для настила в месте сварки.
В процессе работы выделяется инфракрасное и ультрафиолетовое излучение, которое может вызвать заболевания глаз. Поэтому для защиты глаз обязательно нужно использовать маски или шлемы со светофильтрами темно-зеленого цвета. Защитное стекло, используемое при сварке, делает неудобным наблюдение за процессом и особенно в момент зажигания дуги. Современная маска сварщика оснащена защитным стеклом-«хамелеоном» с сенсорным эффектом: степень пропускания им света резко уменьшается при зажигании дуги, причем эту степень пропускания можно отрегулировать самому.
Сварочная пыль также оказывает на человека отрицательное воздействие, по этой причине работа должна производиться только в специальной одежде из плотного брезента, в отдельных случаях в респираторе.
Электроды
Для получения высококачественного сварного соединения используют электроды, покрытые специальной обмазкой. Назначение обмазки — продуцирование шлака с металлическими окислами и защита металла шва от соприкосновения с воздухом во время сварки. Кроме того, обмазка пополняет убыль элементов, выгорающих в дуге, а также вводит в шов новые элементы. Наконец, обмазка повышает устойчивость горения дуги. Более того, шлаковый покров замедляет остывание металла, что способствует выделению из него газов, в результате чего шов получается более прочным.
Электроды для электродуговой сварки можно разделить на две основные группы: плавящиеся и неплавящиеся. Неплавящиеся электродные стержни изготавливают из вольфрама, электротехнического угля или синтетического графита. Угольные и графитовые стержни бывают диаметром от 4 до 18 мм, длиной 250 и 700 мм. Графитовые электроды имеют лучшую электропроводность и более стойки против окисления при высоких температурах, чем угольные.
Плавящиеся электроды бывают стальные, чугунные, алюминиевые, медные и др. Их изготавливают из сварочных проволок. Преимущественное применение имеют стальные электроды, стержни которых делают из электродной проволоки диаметром от 1,6 до 12 мм и длиной от 150 до 450 мм.
Покрытые металлические электроды для ручной электродуговой сварки и наплавки сталей классифицируются по группам и имеют соответствующую маркировку:
В — для сварки высоколегированных сталей с особыми свойствами (49 типов);
Л — для сварки легированных конструкционных сталей с временным сопротивлением разрыву 600 МПа (5 типов);
Т — для сварки легированных теплостойких сталей (9 типов);
У — для сварки углеродистых и низколегированных конструкционных сталей с временным сопротивлением разрыву;
Н — для наплавки поверхностных слоев с особыми свойствами (44 типа).
Электроды подразделяют на типы: Э-38, Э-42, Э-46, Э-50, их применяют для сварки углеродистых и низколегированных конструкционных сталей с временным сопротивлением разрыву до 500 МПа (числа в обозначении типа электрода указывают минимальное гарантируемое временное сопротивление разрыву металла шва в кгс/мм3); Э-42А, Э-46А, Э-50А применяют для сварки углеродистых и низколегированных сталей, когда к металлу сварного шва предъявляют повышенные требования по пластичности и ударной вязкости. Существуют также электроды для ручной электродуговой сварки с особыми свойствами, но в любительской практике их, как правило, не применяют.
Электроды подразделяют по толщине обмазки в зависимости от отношения диаметра покрытого электрода D к диаметру сварочной проволоки d:
М — с тонким покрытием (D/d=l,2); С — со средним покрытием (1,2/d,45); Д — с толстым покрытием (l,45/d,8); Г — с особо толстым покрытием (D/d1,8).
Электроды с тонким покрытием применяют для сварки неответственных швов, от вредного воздействия кислорода и азота воздуха они не защищают. В качестве обмазки для тонких покрытий часто применяют смесь 80 массовых частей молотого мела и 20 массовых частей жидкого стекла, разведенных в воде до консистенции сметаны. Толщина такого покрытия составляет 0,1-0,5 мм. Электроды со средним, толстым и особо толстым покрытиями изготавливают методом спрессовывания или окунания с последующей сушкой и прокаливанием. В состав толстых покрытий входят стабилизирующие (соединения кальция, натрия), связующие (жидкое стекло), шлакообразующие (марганцевая руда, каолин), раскисляющие (ферросилиций), газообразуюшие (древесная мука, декстрин) и легирующие (феррохром) компоненты.
Электроды подразделяют по видам покрытия:
А — с кислым покрытием; Б — с основным покрытием; Ц — с целлюлозным покрытием; Р — с рутиловым покрытием; П — с прочими видами покрытия.
Если условное обозначение состоит из двух букв, значит, покрытие смешанного типа. При наличии в составе покрытия железного порошка в количестве более 20% к обозначению вида покрытия электрода добавляют букву Ж.
Кислые покрытия состоят из окислов кремния, марганца и железа, основные покрытия содержат мрамор и плавиковый шпат, целлюлозные — целлюлозу, а рутиловые в качестве основного элемента содержат рутил. К прочим покрытиям относятся органические обмазки, содержащие крахмал, муку пищевую и т.д.
Электроды с кислым покрытием применяют при сварке швов в любом пространственном положении, с ржавыми кромками и окалиной, переменным и постоянным током. Электроды с основным покрытием используют при сварке постоянным током обратной полярности во всех пространственных положениях шва. Эти электроды чувствительны к ржавчине, влаге и другим загрязнениям свариваемых кромок. Электроды с целлюлозным покрытием используют при сварке постоянным током любой полярности. Электроды с рутиловым покрытием обеспечивают хорошее формирование шва, устойчивое горение дуги при сварке постоянным и переменным током.
Электроды подразделяют по допустимым пространственным положениям сварки и наплавки:
1 — для всех положений; 2 — для всех положений, кроме вертикального сверху вниз; 3 — для нижнего, горизонтального на вертикальной плоскости и вертикального сверху вниз; 4 — для нижнего.
Электроды маркируют на упаковочных этикетках, пачках, коробках или ящиках. Рассмотрим пример расшифровки обозначения электродов:
Э-46-УОНИИ-13/45-4,0-УД2 Е432(6)-Б1
Указанная марка обозначает, что это электроды типа Э-46, марки УОНИИ-13/45, диаметр 4 мм, для сварки углеродистых и низколегированных сталей (У), с толстым покрытием (Д), второй группы по качеству, с установленной группой индексов, характеризующих наплавленный металл и металл шва (432(6)), с основным покрытием (Б), для сварки во всех пространственных положениях.
Верхние торцы металлических электродов окрашивают в следующие цвета:
красный — электроды общего назначения для сварки углеродистых и низколегированных конструкционных сталей, более 90% всех выпускаемых электродов составляет эта группа; синий — электроды для сварки теплоустойчивых сталей; желтый — электроды для сварки коррозионностойких и жаропрочных сталей; сиреневый — электроды для сварки высокопрочных среднелегированных сталей; оранжевый — электроды для наплавки металла на детали; зеленый — электроды для сварки и наплавки чугуна; серый — электроды для сварки цветных металлов.
Наиболее ходовыми являются универсальные сварочные электроды соответствующего диаметра с рутиловым покрытием марок АНО-3, АНО-4, МР-3, МР-4, ОЗС-3, ОЗС-4. Они подходят для сварки конструкций из углеродистых и низколегированных сталей переменным и постоянным током. Для сварки высоколегированных сталей (нержавеющей, жаростойкой), алюминия и его сплавов, меди и ее сплавов используют не только специальные электроды, предназначенные для сварки постоянным током, но и соблюдают определенную полярность их включения, указанную на упаковке,— прямую или обратную. Если вы не исключаете возможность сваривать эти материалы в домашнем хозяйстве, то при покупке сварочного аппарата поинтересуйтесь, предусмотрено ли для него использование соответствующих электродов.
Малогабаритные сварочные аппараты
Самостоятельно сделать прочную конструкцию из металлического уголка или швеллера (шкафчик для инструмента или для газовых баллонов, каркас скамейки или парника, ворота или калитку), отремонтировать садовый инвентарь удобнее всего с помощью сварки. При необходимости приобрести сварочный аппарат многих смущают внушительные габариты и другие неудобства в его использовании в домашнем хозяйстве.
В нашей энциклопедии представлен большой выбор самодельных конструкций сварочного и газосварочного оборудования (см. раздел "Домашнему мастеру").
Кроме того, в последнее время в продаже появились бытовые сварочные аппараты, которые настолько меньше промышленных по массе и размерам, что кажутся почти игрушечными. Их можно переносить за специальную ручку или на ремне через плечо без особых усилий. Поэтому не будет проблем при выделении места для постоянного хранения такого аппарата. Работа же с ним настолько проста, что каждый желающий может овладеть искусством сварки.
В этой статье мы ограничимся рассмотрением малогабаритных сварочных аппаратов массой до 20 кг (это делает доступным перенос их одной рукой), рассчитанных на pa-боту от электросети напряжением 220 В, которая имеется в каждом доме.
Температура в зоне дуги обычно доходит до 6000—7000 °С и определяется силой сварочного тока, которая при ограниченной массе сварочного аппарата не превышает 160—200 А. Для достижения такой силы тока напряжение на выходе сварочного аппарата снижают до 48-90 В (напряжение холостого хода Uхх), этого достаточно для зажигания дуги и безопасно для жизни сварщика. Напряжение снижают с помощью понижающего трансформатора, являющегося неотъемлемой частью сварочного аппарата. Чем больше сила тока при достаточном Uхх, тем больше может быть диаметр электрода, а чем больше диаметр электрода, тем массивнее могут быть свариваемые детали. В табл.1 приведены примерные соотношения между толщиной свариваемого металла, диаметром электродов и силой сварочного тока.
Таблица 1. Соотношения толщины свариваемого металла с диаметром электрода и силой сварочного тока

Чтобы обеспечить такую силу тока, сердечник трансформатора делают массивным, а провод вторичной обмотки — толстым (с площадью сечения более 10 мм2). Силу тока при сварке разных материалов приходится подбирать из приведенных в таблице диапазонов, вот почему должно быть предусмотрено устройство для изменения силы тока, а для исключения перегрева встраивают один или несколько вентиляторов. Все это увеличивает массу бытового сварочного аппарата, поэтому производителям приходится придумывать способы ее снижения.
Самый простой способ — ограничение времени работы трансформатора. Специальный показатель ПН — продолжительность нагрузки, измеряется в процентах по отношению к циклу сварки (в России этот цикл — 5 мин, а в Европе — 10 мин). Например, при ПН = 60% процесс осуществляется следующим образом: 3 мин — сварка, 2 мин — остывание трансформатора, затем цикл сварки повторяется, а при ПН = 20% — 1 мин сварка, а 4 мин остывание трансформатора. Этот показатель должен быть приведен в любом паспорте на сварочный аппарат, причем при максимальной силе сварочного тока для каждого аппарата ПН = 20—60%, а при наименьшей силе тока ПН = 100% и обеспечивает непрерывную сварку.
Однако, стремясь уменьшить время простоя трансформатора, нельзя забывать, что прерывание процесса иногда просто необходимо. Во-первых, для периодической установки в электрододержатель нового электрода вместо использованного, а во-вторых, после 3—5 мин непрерывной сварки обычно возникает необходимость подготовки деталей для дальнейшей работы. При продолжительной же сварке, например, изгороди из сетки «рабица» с уголковым каркасом, эти перерывы мешают. Чтобы мастер не увлекся сваркой и не сжег трансформатор, многие аппараты оснащены устройством термозащиты для автоматического отключения от электросети в случае перегрева.
Гораздо проще осуществляется РДС на постоянном токе, поскольку в этом случае на дугу меньше влияет частота напряжения сети. Для преобразования тока из переменного в постоянный после трансформатора устанавливается полупроводниковый выпрямитель, к которому добавлены элементы для сглаживания пульсаций выпрямленного тока. Все это значительно увеличивает массу и снижает надежность аппарата. Но есть и свои преимущества: в сварном шве присутствует больше «родного» металла деталей, чем присадочного металла электродов, в результате чего уменьшается количество окалины и, как следствие, обеспечивается более качественное соединение по сравнению с РДС на переменном токе. Сокращаются также стоимость работ и расход электродов. Такой аппарат называют сварочным выпрямителем. Им проще работать, но стоит он дороже сварочного трансформатора в 1,5—4 раза.
Все более широкое распространение находят инверторные сварочные выпрямители (инверторы), в которых перед усилением сначала повышают частоту переменного тока до 10—90 кГц. Масса и размеры высокочастотных трансформаторов существенно меньше, чем у их 50-герцевых собратьев. Эта особенность позволяет значительно уменьшить габариты всего инверторного аппарата по сравнению с обычными сварочными трансформаторами и выпрямителями. Ток после инвертора практически постоянный и не зависит от колебаний длины дуги и напряжения, поэтому его силу можно регулировать плавно и подбирать довольно точно. Дугу также можно подбирать от самой «мягкой», которая легко «тянется», до «грубой», которую обычно используют при резке металла. Это позволяет даже непрофессионалу легко освоить сварку, в том числе «капризных» алюминиевых и медных сплавов, или высоколегированной, например, нержавеющей стали.
Существуют инверторы небольшого размера и массой до 10 кг, их можно носить на ремне через плечо и подключать в общую электрическую сеть через предохранитель на 16 А, конечно, с обязательным заземлением корпуса. Но стоимость их самая высокая: в 4—9 раз выше, чем сварочных трансформаторов. На российском рынке можно найти все перечисленные виды сварочных аппаратов для РДС французской фирмы «SAF», финской «Kemppi», австрийской «Fronius», итальянских «Cebora», «Telwin», «Deca», шведской «Esab», американской «Miller», а также российских производителей — ООО «ЭВМА», ТОО «Линкор», ООО «ТОР», АО «Невская Электрическая Компания».
Экономичность работы аппарата характеризуют коэффициентом полезного действия (КПД) в процентах (чем он ближе к 100%, тем дешевле обходится сварка), и коэффициентом мощности (cos ф) (он должен быть как можно ближе к единице). Следует отметить, что КПД и cos ф характеризуют тщательность проработки конструкции сварочного аппарата, поэтому не все фирмы приводят эти значения в паспорте на аппарат.
Для регулирования силы сварочного тока используют устройства с органами управления и со шкалой на панели аппарата, проградуированной либо в амперах, либо в номерах диапазонов (1,2,3,...), либо в диаметрах электрода. В наиболее простых моделях силу тока можно менять переключателем только ступенчато, а в более сложных — плавно, с помощью поворачивающейся рукоятки.
Ряд моделей имеют устройства плавноступенчатого регулирования силы тока: сначала устанавливают соответствующий диапазон изменения силы тока переключателем, а затем более точно подбирают нужную его величину в пределах этого диапазона поворачивающейся рукояткой. Такие устройства увеличивают стоимость сварочного аппарата на 15-20%. Иногда на панели устанавливают амперметр для фиксации точной величины сварочного тока.
Ресурс работы бытовых сварочных аппаратов рассчитан на 250—350 ч работы, после чего обычно необходим профилактический ремонт (перемотка или замена сгоревшего трансформатора, замена выключателя или регулятора сварочного тока и т.д.). Промышленные переносные аппараты («Transpocket 1400», «Master 1500», «Caddy 130») прослужат без ремонта намного дольше, но они существенно дороже бытовых. Для наглядности сравним сварочный трансформатор «Сварис» (35 кг, размеры 310x280x510 мм) со сварочным выпрямителем «Терминатор». «Терминатор» обеспечивает более высокую силу сварочного тока при габаритах в 3,5 раза и массе почти в 3 раза меньших, чем у «Свариса», при этом сохраняет возможность запуска двигателя автомобиля, но стоит такой аппарат почти в 2 раза дороже.
Таблица 2. Переносные аппараты на 220 В для ручной дуговой сварки одиночным электродом
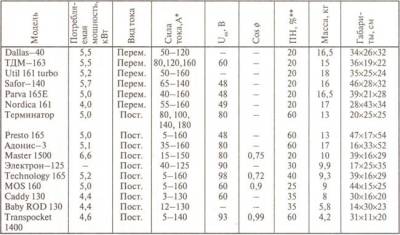
Примечание. Кроме моделей ТДМ-163 и «Терминатор» во всех перечисленных в таблице моделях есть защита от перегрева; * значения силы тока, указанные через запятую, могут быть установлены на сварочном аппарате ступенчато, а через тире — плавно или плавноступенчато; ** значения ПН приведены для максимальной силы сварочного тока.
Рекомендации по использованию сварочных аппаратов
В инструкциях по использованию некоторых сварочных аппаратов вместо показателя ПН приведен показатель ПВ — продолжительность включения. Пусть это вас не смущает: его значение полностью совпадает со значением показателя ПН.
Инверторы более чувствительны к уменьшению напряжения в сети, чем сварочные трансформаторы и выпрямители: при снижении напряжения на 15% такой аппарат просто не запускается.
Любой аппарат следует обязательно периодически использовать (хотя бы раз в 3 месяца), поскольку при отсутствии тока в его отдельных элементах, например в конденсаторах, происходят процессы, снижающие работоспособность аппарата.
При преимущественном использовании электродов одного диаметра, например 3 мм, лучше приобрести сварочный аппарат, у которого для них ПН = 100%.
Установите предохранитель, рассчитанный на ток не менее 16 А, и подводящий провод с сечением не менее 2,5 мм2 при максимальной силе сварочного тока до 140 А, или отдельный щиток с электросчетчиком, рассчитанным на ток не менее 40 А, например модели СО-И-446М, и подводящим проводом с сечением не менее 6 мм2 при максимальной силе сварочного тока от 160 до 300 А.
При выборе места для щитка учтите, что длина соединительного кабеля от этого щитка к сварочному аппарату должна быть ограничена. Она обязательно указывается в паспорте на аппарат и составляет обычно от 5 до 15 м.
Технология сварки электрической дугой
Качество сварного соединения зависит от подготовки сборки заготовок под сварку и режима сварки. Основной металл в разделке свариваемых кромок и на 20—30 мм от них должен быть тщательно очищен от ржавчины и других загрязнений. Режим сварки характеризуется совокупностью параметров, определяющих условия процесса. При ручной электродуговой сварке основными параметрами являются: диаметр электрода, сила тока, его род и полярность, напряжение на дуге, скорость перемещения электрода. К дополнительным факторам относятся: положение электрода и шва в пространстве, состав и толщина электродного покрытия, начальная температура свариваемых деталей.
Ширина сварного шва зависит от диаметра электрода. Диаметр электрода при сварке горизонтальных швов выбирают, пользуясь следующими, установленными практикой, данными из табл. 3.
Таблица 3. Выбор диаметра электрода для сварки горизонтальных швов в зависимости от толщины металла

При сварке вертикальных швов не следует пользоваться электродами диаметром более 5 мм, а при сварке потолочных швов — более 4 мм. Электроды диаметром более 6 мм применяют редко. Тип и марку электрода можно выбрать по справочным таблицам в зависимости от марки свариваемого металла и условий сварки. Химический состав металла электрода должен быть одинаковым с химическим составом свариваемого металла или близким к нему.
Силу сварочного тока Iсв (А) можно ориентировочно определить по формуле:
Iсв = Kdэл ,
где dэл — диаметр электрода, К — опытный коэффициент, равный 40—60 мм для электродов со стержнем из низкоуглеродистой стали и 35—40 мм для электродов со стержнем из высоколегированной стали. Величина сварочного тока зависит также от вида сварочного соединения: нахлесточные и тавровые соединения выполняют повышенным током по сравнению со стыковым. Сварочный ток зависит от марки электрода и может быть определен более точно по справочным таблицам.
Для возбуждения дуги необходимо электродом коснуться поверхности изделия — получается короткое замыкание, затем отвести его на нужное расстояние (2—4 мм), при этом нагретый воздух становится проводником. Существует еще один способ зажигания электрической дуги — так называемое чирканье электродом по металлу, как спичкой, но его нельзя применять в неприспособленных для сварки местах.
Качество сварного шва зависит от длины дуги. Умение поддерживать ее в оптимальном состоянии приходит с опытом, но рекомендуется придерживаться существующего правила: расстояние от электрода до кромки свариваемой поверхности должно составлять 0,5—1,1 диаметра применяемого электрода. Это расстояние между электродом и свариваемыми кромками необходимо поддерживать, поскольку при их касании происходит короткое замыкание, а при слишком большом зазоре дуга гаснет.
Перемещение электрода необходимо для поддержания горения сварочной дуги и получения сварного шва. Сварщик в процессе работы должен делать три движения электродом: непрерывное равномерное вниз по мере расплавления электрода, в направлении сварки и поперек шва. Поперечные колебательные движения конца электрода можно не делать при сварке тонких листов.
Сварку можно производить в направлении слева направо (рис. 4, а), справа налево (рис. 4, б), от себя (рис. 4, в) и к себе (рис. 4, г). Независимо от направления сварки положение электрода должно быть определенным, электрод должен быть наклонен к оси шва так, чтобы металл свариваемого изделия проплавлялся на наибольшую глубину. При сварке на горизонтальной плоскости для получения ровного и плотного шва угол наклона электрода должен быть равен 15° от вертикали в сторону ведения шва.
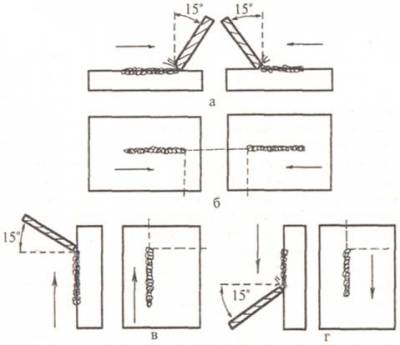
Рис. 4. Направления сварки: а — слева направо; б — справа налево; в — вверх, или от себя; г — вниз, или к себе.
Скорость сварки выбирают с таким расчетом, чтобы получить сварной шов шириной около полутора диаметров электрода, с хорошим проваром и плавным переходом наплавленного металла к поверхности свариваемого изделия.
Очень важно правильно закончить сварной шов. Нельзя резко обрывать дугу. Следует медленно вести ее до обрыва, при этом расплавленный электродный металл должен заполнять кратер шва.
Существует три основных вида швов: горизонтальный, вертикальный и потолочный. Вертикальный шов можно делать на спуск и на подъем. Наиболее эффективна сварка на подъем. Она позволяет проварить корень шва и кромок. Недостаток этого способа — грубая поверхность шва. Сварка на спуск легче, но качество провара ниже. Более сложным в исполнении является горизонтальный шов. Для его выполнения делается скос верхней кромки, а нижняя при этом помогает удерживать расплавленный металл в месте сварки. Самым сложным является потолочный шов. При его выполнении сварка должна производиться очень короткой дугой, а оптимальный диаметр электрода — 4 мм. В процессе работы происходят короткие замыкания в месте соприкосновения конца электрода с изделием и расплавленный металл заполняет сварочную ванну изделия.
В зависимости от того, сколько проходов понадобится для заполнения сечения шва, он может быть однослойным, многослойным и многослойно-многоходным. Шов называется многослойным, если число слоев равно количеству проходов дугой (используется в стыковых соединениях). Многопроходным называется шов, в котором некоторые слои делаются за несколько проходов (применяется в угловых и тавровых соединениях). По длине швы делятся на короткие (до 300 мм), средние (300—1000 мм) и длинные (более 1000 мм).
Сварка может выполняться несколькими способами. Самой простой является сварка напроход — от начала до конца шва (рис. 5, а). Обратноступенчатым способом (от середины к концам) делается шов средней длины (рис. 5, б). Для выполнения длинных швов применяется вышеназванный способ (при этом весь шов разбивается на небольшие участки — рис. 5, в), а также сварка вразброс. Способы «горка» (рис. 5, г) или «каскад» (рис. 5, д) используются для соединения конструкций, несущих большую нагрузку. В этом случае вся сварочная зона должна пребывать в горячем состоянии во избежание появления трещин.
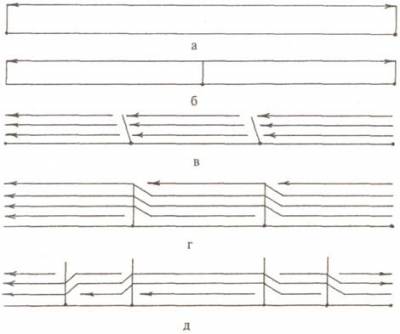
Рис. 5. Схемы различных способов сварки: а — сварка напроход; б — обратноступенчатая сварка; в — сварка блоками; г — «горка»; д — «каскад».
Каждый способ сварки осуществляется в определенном режиме. Его параметры делятся на основные (величина и полярность тока, диаметр электрода, скорость сварки, напряжение на дуге) и дополнительные (положение электрода и изделия, состав электрода). В своей совокупности они оказывают большое влияние на весь сварочный процесс.
В любительской практике наиболее распространенный способ сварки — сварка встык. Для усиления стыковых соединений в ответственных конструкциях применяют накладки с одной или двух сторон. Накладки делают в форме вытянутого шести- или восьмиугольника. Применять накладки прямоугольной формы нецелесообразно, так как по углам возникают большие внутренние напряжения. Накладка должна перекрывать сварной шов не менее чем на 100 мм. При установке накладок с двух сторон их следует брать различной величины, чтобы кромки их не совпадали и одна из них перекрывала другую на 20-30 мм.
При сварке внахлестку величина перекрытия должна быть не менее пятикратной толщины свариваемого металла.
Важно помнить, что некоторые металлы требуют сварки только с использованием постоянного тока прямой полярности, а магний, алюминий и бериллий — переменного.
Чтобы проверить качество шва, удаляют окалину молотком сварщика. У начинающих наиболее часто встречается непровар (не полностью проваренный сварной шов). Если такое случилось, изъян устраняют.
Сварка тонколистовой стали
Главной трудностью при ее выполнении является появление прожогов. Во избежание этого сварка производится на минимальном токе (50-70 А) электродами малого диаметра (1,6-2,0 мм), а также делаются отбортовки краев свариваемых изделий. При приваривании толстого листа к тонкому необходимо следить за тем, чтобы переход с одного листа на другой получался плавный.
Сварка чугуна
Она может осуществляться двумя способами: горячим и холодным. Горячая сварка предполагает предварительную очистку свариваемых деталей, их формовку и подогрев до температуры 600—800 °С. Затем делается сама сварка и изделие медленно охлаждается. Недостаток горячей сварки чугуна — трудоемкость процесса. Холодная сварка включает очистку деталей, разделку кромок свариваемых поверхностей, сварку и последующую проковку. Проковка делается для того, чтобы снизить опасность появления трещин в околошовной зоне. При выполнении холодной сварки используются стальные, никелевые, медно-никелевые, медно-железные и железоникелевые электроды.
Сварка цветных металлов и сплавов
При сваривании изделий из меди возникают некоторые сложности. Во-первых, в составе этого химического элемента всегда присутствуют примеси. Во-вторых, в расплавленном состоянии медь окисляется и в большом количестве поглощает водород, что ведет к появлению пузырьков воды в свариваемом участке. А это в свою очередь снижает пластичность и прочность изделия. Чтобы избежать подобного, нужно уменьшить количество водорода в зоне сварки, для чего используют защитные газы и прокалку электродов. Необходимо также использовать флюсы, которые позволяют растворить образующиеся оксиды. В состав таких флюсов входят борная кислота, калий фосфорнокислый, бура прокаленная, древесный уголь, поваренная соль, кварцевый песок и поташ. Сварка меди производится преимущественно электродами марки АНЦ-1 и АНЦ-2.
При сваривании бронзы используются различные технологии, что вызвано наличием большого количества ее видов (оловянистые, кремнистые, фосфористые и др.). Сварка бронзы производится постоянным током обратной полярности несколькими короткими швами.
Сварка изделий из латуни (сплав меди с цинком) проводится также короткой дугой постоянного тока обратной полярности, но требует обязательной последующей проковки шва и отжига при температуре 600—660 °С для выравнивания химического состава латуни.
При сварке алюминия и его сплавов возникает ряд сложностей. Во-первых, в процессе сварки на поверхности расплавленного металла появляется пленка оксида алюминия, мешающая сплавлению частей изделия. Поэтому сначала необходимо тщательно очистить края деталей и электрод. Обезжиривание и травление, производимые для удаления оксидной пленки, нужно делать за 2—4 ч до начала самого процесса. Скорость сварки алюминия достаточно высока, рекомендуется выполнять ее одним электродом. Предварительный подогрев и применение постоянного тока обратной полярности позволяют осуществлять нужное проплавление изделия.
• Сварочный ток зависит от напряжения сети и при падении последнего до 180—200 В следует перейти на сварку электродом меньшего диаметра. • При наличии амперметра на панели управления сварочным аппаратом можно запомнить точное значение подобранного тока при сварке какого-либо металла и в дальнейшем сразу устанавливать это значение при подобных работах, сократив этим время на подбор режима.
Автор-составитель. Патлах В.В. http://www.patlah.ru
|